Unlocking the Future of Industry XR and Digital Twins in Manufacturing
- viroinnovation
- Feb 20
- 3 min read
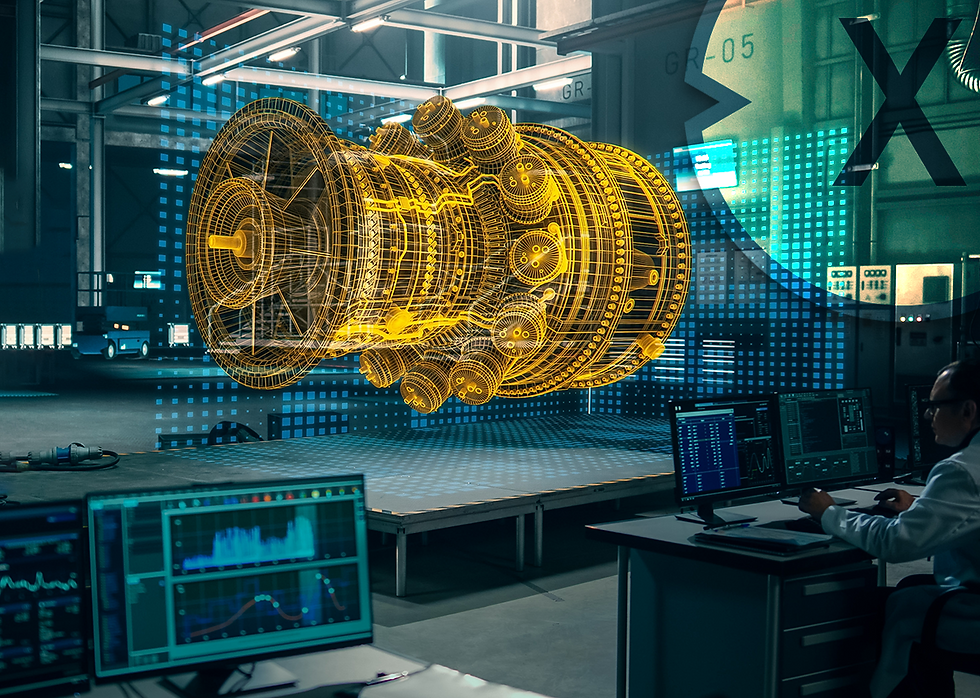
The Role of Digital Twins in Manufacturing
The fourth industrial revolution or Industry 4.0 relies on digital twins. These virtual tools allow technicians to visualize products and factory processes, collaborate with team members worldwide, and receive executive sign-off before a physical product exists. Digital twins are a crucial component of modern manufacturing processes.
What Are Digital Twins in Manufacturing
Businesses use digital twins in construction manufacturing factory planning and more to replicate real-world buildings heavy equipment and products in a virtual environment. With XR headsets and controls, workers get a life-like view of objects at a one-to-one scale and understand their relationship to product design.
Teams interact with virtual objects test features and processes and make decisions faster and at lower costs. Some digital twins are so detailed that users point to a single bolt within a product and instantly see who made it how much it cost its specifications manuals and more. Organizations use XR-enabled digital twins to enhance
Prototyping
Product design
Factory planning
Project planning
Human factors and ergonomics
Critical skills training
Familiarization and safety training
Warehousing
Sales and marketing
Simulation
Maintenance
Renovation and decommissioning
Speed Up Product Development
Product development is complex and time-consuming requiring coordination across multiple teams to research and develop prototypes through multiple revisions. Many of these teams are in different cities or countries requiring extensive travel for product presentations and executive sign-offs.
By integrating digital twins into XR environments businesses streamline the entire product development chain reducing prototyping and decision-making time.
John Maxfield business development director at VR solution provider Virtalis considers digital twins as essential as video conferencing software
Businesses need to be able to effortlessly collaborate not just in the same room but in a distributed environment as well Digital twins allow teams to join a virtual workspace and have dynamic conversations just like they do with Teams or Zoom today
Virtalis works with major manufacturing companies including Ford Motors Siemens Rolls-Royce and Airbus. Their biggest success with digital twins is in collaborative design review leading to
45 percent faster project times
40 percent reduction in project costs
30 percent decrease in product development time
67 percent increase in design sign-offs using digital twins
Enhance Training Outcomes
Building real-world manufacturing training scenarios is expensive time-consuming and difficult to scale. Digital twins provide
Greater flexibility
Improved knowledge retention
Faster training development
Safe and immersive learning environments
Typical training scenarios include
Training teams on new assembly or manufacturing processes
Practicing maintenance tasks and testing new procedures
Training customers on standard operating procedures for large equipment
Simulating emergency situations and hazardous environments
Maxfield highlights the training impact seen by Virtalis clients
78 percent improved retention of assembly and maintenance processes
40 percent faster knowledge acquisition
40 percent reduction in training costs
30 percent reduction in training time
Optimize Factory Layouts and Worker Ergonomics
Maxfield notes that digital twin technology for factory layout planning is one of the fastest-growing use cases for XR
With digital twins we create a virtual model of an entire factory to test and validate layouts material flows manufacturing cells and process efficiencies all without disrupting any physical operations
Beyond improving factory operations digital twins play a major role in worker ergonomics XR users
Visualize ergonomic risks in real-time
Simulate physical strain based on worker height and reach
Optimize workstation and tool placement to reduce injuries
With digital twin simulations manufacturing plants report
80 percent reduction in reported issues
25 percent reduction in time to adapt work cells
50 percent faster product time to market
70 percent reduction in production line injuries
Comments